3D Printed MagSafe Dock
Click here to download PDF report (highest quality)
Click here to download PDF report (lower quality)
Background
With the introduction of the iPhone 12, Apple introduced MagSafe charging. The update boosts charging speeds from 7.5W with the Qi charger to now up to 15W. This is achieved through a ring of magnets in the back of the iPhone that allow the charging coils to concentrically align with the charging puck. The charger conveniently snaps onto the phone with very strong adhesion. The advantages of the MagSafe charger are both the charging speed and that the magnets are self aligning. This ensures that your device makes contact with the charging coils so intentional placement is not as necessary.
Current Available Products
However, this design does not accomplish the original goal of MagSafe for Apple’s laptops - the phone will come crashing down from a table if the cable is yanked. In order to remove the charger, you have to “peel” the puck off the phone using both hands. Current aftermarket products utilize the strong connection and turn the system into a charging stand. Although they might claim a one-hand operation, the user would still need to hold the base of the stand in order to overcome the magnetic force. Without being weighed down or anchored, these adapters do not address the need for a true docking system.
Project Plan
Objective
Rapidly prototype an iPhone stand to be used in conjunction with the Magsafe charging puck and create an anchored docking system.
Scope
The stand must house the Magsafe charging puck through an interference fit. To make this requirement, the axial holding force will need to exceed the force necessary to remove the iPhone.
The stand must be a true docking system so that it will stay in place when placing and removing the iPhone. The user must be able to place the remove the iPhone from the stand with one hand.
Tasks
A. Model a triangular shaped stand in Fusion 360 compatible with any phone.
Test dimensions to ensure height of phone and viewing angle are acceptable.
B. Adjust model and test as-built (3D printed) size of Magsafe hole to achieve interference fit.
I expect shrinkage to occur due to the contraction of PLA from 220C to room temp.
C. Ensure charging puck does not come out of stand during removal of phone.
D. Estimate the axial holding force of the charging puck in the stand.
Gather axial interference fit equation.
Research material properties for Fused Filament Fabrication (FFF) PLA and rare- earth magnets for Magsafe.
E. Devise test criteria to estimate the force required to remove the iPhone from the Magsafe charging puck.
F. Sketch free body diagram to design an anchoring system for the stand to a table surface.
Analyze this result to determine method of anchorage.
G. Adjust the model to accommodate an anchoring system.
Research anti-slip attachments, weighted systems, and alter design to accommodate.
H. Test the stand on multiple surfaces to ensure versatility.
Regular Stand for Overall Geometry
Modeling in Fusion 360
I designed a triangular stand for aesthetic symmetry and future adjustability. I estimated the viewing angle and the clearance beneath the phone as shown in red. The slots down the center allow a charging cable to be fed through the back.
Printing
I printed the stand sideways to minimize the z-axis height to the 80mm width. Additionally, this orientation would reduce the amount of overhang needing support. The viewing angle recognized face ID and the clearance beneath the phone was acceptable for the charging cable. The only issue was that the supports shown below in green were extremely difficult to remove.
It turns out this was just a leftover setting from a previous project so I adjusted the contact z distance from 0.05 to the default 0.10mm. This would increase the gap between support material and the part - ensuring that the part would not fuse to the support.
Incorporating the MagSafe Charger
Modeling in Fusion 360
I altered the design to include a wider base to accommodate for the increased overall height. I now needed to create an interference fit for the Magsafe charging puck. However, I did not want to print out full models just to dial in the hole diameter. I utilized PrusaSlicer to trim down the part to isolate the hole and cable slot.
Printing
I started with 55.75mm diameter blind hole with a 5.4mm depth to get a sense for the shrinkage likely to occur with the contraction of the PLA. The first test part did not have a large enough slot for the charging cable to fit through. Additionally, the hole for the charging puck had shrank to 55.23mm, slightly less than 1%. I was unable to fit the charging puck into the hole at this dimension. I went on to increase the size of the slot for the USB-C cable and tried a design of 56.2 and 56.1mm which shrank by about 0.5% each. I found that 56.1mm which reduced to 55.77mm was snug enough to support the phone yet easy enough to remove by pressing it out from the back.
Calculations for Axial Holding Force
Axial Holding Force equation, Constants, Diagram
The sources for material properties for rare earth magnets and FFF (Fused Filament Fabrication) PLA can be found here at the end of the report. Tensile testing was done on PLA and the friction coefficient was done with a pin on disc tribometer.
Assumptions
Cold creep of PLA not factored in because stress would not be reoccurring
d is nominal diameter with a value of 55.88mm because the Magsafe is designed in
CA using inches (2.2”); my measured value of the Magsafe was 55.90mm (double
checked on Reddit that others also got this value)
The USB-C slot does not allow significant flexing of the material
• The arc length only accounts for just over 4mm, or about 2.27% of the total circumference
The usable cylinder diameter outer (d,o) is 2mm - average gap between hole and end of part
Friction coefficient between FFF PLA and steel is equivalent to FFF PLA and Magsafe changing puck.
Magnetic Force Testing
The next step was to test the force required to detach the phone from MagSafe. I utilized my previous test parts to create a weighted test using the following:
1000g weight set
(2) sawhorses
(2) wooden particle boards
(4) string ties
Food scale
Weight test for detachment force - failure at 654g
I set up an iPhone 12 between two wooden particle boards with a microfiber cloth to level out the the camera protrusion. The MagSafe charger was placed in the test part which was connected to another test part by four zip ties. I found that the total load to overcome the magnetic force was 654g or 1.44lbf. This was 565g of weights plus 89g for the testing apparatus (MagSafe, zip ties, and test parts).
MagSafe Design
After verifying that the force to remove the iPhone was 1.44lbf while the interference fit at 56.1mm (modeled) would require 6.29lbf to engage or disengage the charging puck, I now needed a way to hold the stand down.
Weighted System
Force balance for static equilibrium
Rubber Feet and Heat-set Inserts
Seeing that I would need to add roughly 3.43 lbf or 1.56 kg of mass to my stand, I decided to explore other options. I looked at rubber isolators, suction cups and eventually found these 1” rubber anti-slip feet on McMaster-Carr. I paired them up with 8-32 heat-set brass inserts because I would not be able to 3D print these fine threads.
Rubber Feet and Heat-set Inserts
Seeing that I would need to add roughly 3.43 lbf or 1.56 kg of mass to my stand, I decided to explore other options. I looked at rubber isolators, suction cups and eventually found these 1” rubber anti-slip feet on McMaster-Carr. I paired them up with 8-32 heat-set brass inserts because I would not be able to 3D print these fine threads.
McMaster-Carr order for rubber feet and heat-set inserts
Before I could update my model and print, I needed to correctly size the holes for these inserts. I began looking at the specification sheet and noticed there was conflicting information in the drawing. I emailed McMaster and they provided me with the correct drawing.
Email inquiry and updated heat-set insert drawing for 8-32 brass 1/4” length
Heat-Set Insert Sizing
I started with the recommended No.2 drill bit size for my test holes which began at 5.6 mm all the way up to 6.2mm. I chose increments of 0.1mm because I would be printing in 0.1mm resolution. The part was printed in a vertical orientation - the same that would used in my MagSafe stand. Additionally, I checked that my perimeter settings had three layers to ensure my inserts would attach to solid material.
I heated up my soldering iron to 220C, the same as my nozzle printing temperature for PLA. This would allow the brass insert to conduct the heat to the surrounding plastic inside the hole. Once the brass inserts starting to sink into the plastic, I only had to apply a small amount of pressure for the insert to sit flush to the face of the test piece.
No burring occurred at 6.0mm diameter
I flipped the part to the back and saw a significant amount of burring at 5.6mm and gradually reduced and stopped at 6.0mm. I selected this as the size for my holes as no burring indicates good adhesion without excess plastic that could potentially get in the threads.
MagSafe Dock with Rubber Feet
Installing the Heat-set Inserts
I added three 6mm holes for my inserts according to the testing I had performed. I estimated that the rubber feet would adhere to the surface enough so I decided to use three in order for the stand to stay balanced. I printed the updated model with the same 0.1mm settings to achieve the 56.1mm diameter hole for the MagSafe charger. I also selected rectilinear infill pattern to speed up the print.
The three rubber feet worked well when I compressed them initially by pushing the stand down. However, they quickly lost suction because my assembly was not heavy enough to apply the required pressure. Please view the demonstration below.
Video Demonstration Rubber Feet Issue
Weighted MagSafe Dock with Feet
Increasing the Mass
I liked the three rubber feet as a minimal way to anchor the dock to most surfaces. I also knew that by increasing the size of the rubber feet would require more weight to keep it anchored. I purchased a 3” diameter suction cup used for frying equipment that required more force to push it down.
I noticed that applying a subtle amount of pressure would engage the three rubber feet I had installed beneath the stand. To be exact, only 300g was needed to compress the rubber feet enough for the device to work as intended - the docking stand would stay anchored when the iPhone was removed.
In a Youtube video I saw, the individual loaded his model into PrusaSlicer, added a color change to the G-code and then altered the G-code to transform the filament reload into a pause with the heat bed extended. This would allow him to insert pellet BB’s or clay into the part before it sealed off the top layer. He chose a sparse (5%) infill in order to make room for the fill material. He was able to increase the mass of his part by 4x. A link to the video is provided below.
However, I saw several issues with this method:
Coordinating the pause would require me to watch the printer when the part was roughly 90% completed
Spilling BB’s or clay would be messy
If the fill material was too close to the top surface layer, it could protrude into the finish
BB’s were not cost effective for the mass - 55g/$1 Amazon Link
Instead I decided I would alter my design to accommodate for a fill material to increase the mass. Since I had the freedom to increase the thickness of the base, I decided the fill material would be best placed there. I decided to go with a mild steel rod as it is widely available and dense enough at 0.00787 g/mm^3.
I procured 1/2” smooth steel rod from Home Depot in 36” length for $7.23. This would only cost 128g/$1. To achieve the 300g needed, I estimated (5) 2.8” length rods which would equate to about 354g. I used (2) sawhorses, (2) bar clamps, hot work gloves, and an angle grinder with a cutoff wheel while measuring with my speed square. I ended up with 331g.
Updating the Model
Since I would not be embedding the rods into my design, I needed to create a hollowed out pocket to store the (5) rods. I increased the base thickness by 10mm and created a 14mm tall slot that would span the entire width of the dock. I also made sure to leave a 3mm clear space between any heat-set inserts.
I added a 5mm thick hatch with a pull tab to close off the pocket. I dimensioned the holes according to the test part I previously made. Lastly, I cut some 8-32 screws to length and rethread with my wire strippers.
Printing the Assembly
I uploaded the two parts of my assembly in Fusion 360 to create separate bodies in PrusaSlicer. I selected honeycomb as my infill pattern as paths do not cross - ensuring that layers would stack on top of each other reducing the chances of a failed print and noise. I chose 10% as my infill density because I would gain mechanical resistance by using the honeycomb pattern so I could afford to lose some density. However, I would select gyroid or rectilinear going forward as the support for the holes may have been weakened by the larger hexagonal voids.
Once the feet were on and the rods were added, the dock really stuck to the table. It has worked on many smooth surfaces and would be great on a desk and even better on a granite countertop.
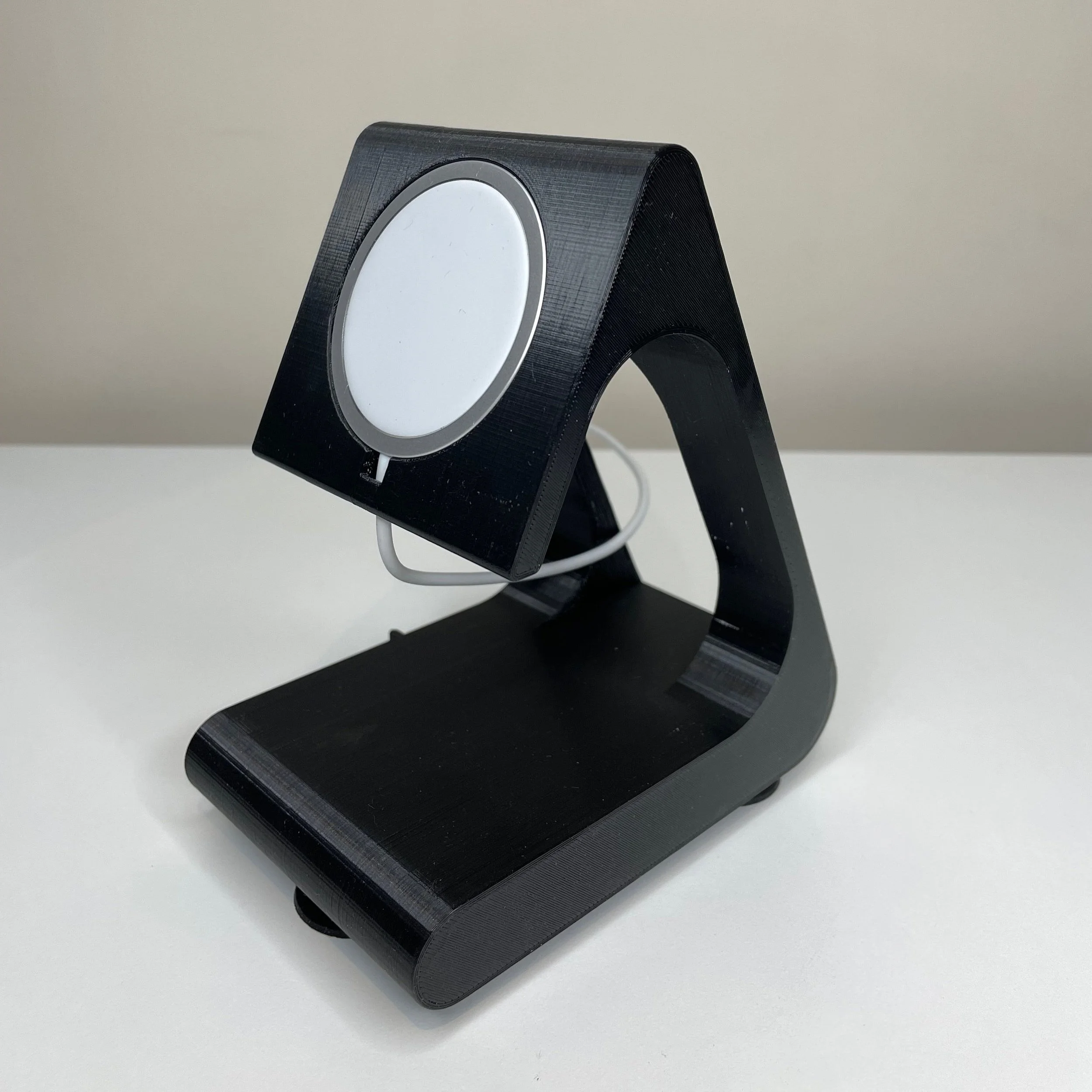



Conclusion
In this project, I successfully designed and 3D printed a docking stand that incorporates MagSafe charging for the iPhone. The dock is one-hand operable and achieves this through three rubber feet and added mass to keep the feet compressed to the table surface. If I were to do this project over again, I would try to reduce my resolution or detail to either 0.15 or 0.2mm because printing at 0.1mm is significantly slower. I think I could have gotten similar results if I had dimensioned the MagSafe hole opening in increments of 0.15mm or 0.2mm. I would have tried to confirm what my tightest tolerance had to be and then used that as my limiting factor. Additionally, when I printed the MagSafe blind hole test parts, I did not factor in that I would be printing my dock in a different orientation. This would slightly alter the diameter of the hole because my stand was printed sideways. I ended up needing to increase the hole from 56.1 to 56.2mm in order get the correct fit.